Gaz (chiffre de 2015)
Pôles de production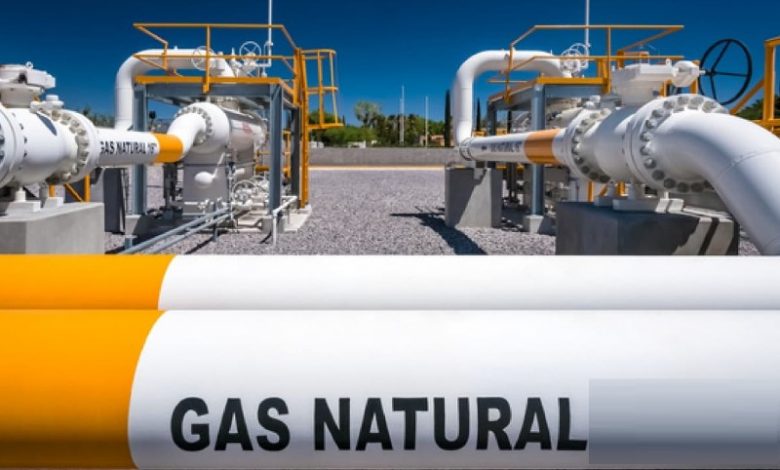
La production des gisements mentionnés plus bas ainsi que les réserves concernent les gaz dits combustibles, c’est-à-dire qu’ils peuvent apporter de l’énergie, exception faite pour le H₂S, qui est un cas à part. Tous les autres gaz, dont le dioxyde de carbone, l’azote, le sulfure d’hydrogène et l’hélium, seront traités dans la partie raffinage.
Production nationale
Information générale :
- Découverte : 1952
- Mise en production : 1953
- Type : Conventionnel Onshore Majeur (1)
- Profondeur : 400 m
- Distance à forer : 400 m
- Réserve en place : 69,4 milliards de m3
- Taux de récupération : 72 %
- Réserve récupérable : 50 milliards de m3
- Réserve déjà produite : 50 milliards de m3
- Réserve extractible restante : 0 milliards de m3
- Production journalière maximale enregistrée : 6,6 millions de m3 par jour
- Temps durant lequel cette production a été maintenue : 6 ans, de 1966 à 1973
- Nombre de puits en activité : 0
- Nombre de puits maximum enregistré en activité : 25
- Production moyenne par puits en activité : 0 m3 par jour
- Production actuelle : 0 m3 par jour
- Fermeture du dernier puits : 2001
Composition du gaz :
- Méthane : 83 %
- Éthane : 8 %
- Propane : 4 %
- Butane : 2 %
- Dioxyde de carbone : 1 %
- Azote : 2 %
- Sulfure d’hydrogène : 0,1 %
- Hélium : 0 %
Le champ gazier d’Alphastern, découvert en 1952 et mis en production en 1953, est le premier gisement découvert sur le sol raskenois. Il s’agit d’un gisement onshore situé à 400 mètres de profondeur, contenant près de 69,4 milliards de mètres cubes de gaz, dont 72 %, soit 50 milliards de mètres cubes, sont exploitables. Il est alors classé dans la catégorie des gisements majeurs(1).
De par sa composition, son gaz est dit humide(4), c’est-à-dire qu’il contient une forte proportion d’hydrocarbures plus lourds que le méthane. De plus, il présente une faible part d’impuretés, représentée par le CO₂, l’azote et le H₂S. Sa production maximale, de 6,6 millions de m³/jour, a été maintenue pendant six ans (1966-1973), avec un maximum de 25 puits actifs. Le dernier puits a été fermé en 2001, et le gisement est aujourd’hui complètement épuisé.
Information générale :
- Découverte : 1958
- Mise en production : 1959
- Type : Conventionnel Onshore Majeur(1)
- Profondeur : 940 m
- Distance à forer : 940 m
- Réserve en place : 44,9 milliards de m3
- Taux de récupération : 78 %
- Réserve récupérable : 35 milliards de m3
- Réserve déjà produite : 35 milliards de m3
- Réserve extractible restante : 0 milliards de m3
- Production journalière maximale enregistrée : 4,62 millions de m3 par jour
- Temps durant lequel cette production a été maintenue : 5 ans, de 1974 à 1979
- Nombre de puits en activité : 0
- Nombre de puits maximum enregistré en activité : 19
- Production moyenne par puits en activité : 0 m³ par jour
- Production actuelle : 0 m³ par jour
- Fermeture du dernier puits : 2006
Composition du gaz :
- Méthane : 87 %
- Éthane : 7 %
- Propane : 3 %
- Butane : 2 %
- Dioxyde de carbone : 0,5 %
- Azote : 0,5 %
- Sulfure d’hydrogène : 0 %
- Hélium : 0 %
Le champ gazier d’Omegaville, découvert en 1958 et mis en production en 1959, est le deuxième gisement découvert sur le sol raskenois. Il s’agit d’un gisement onshore situé à 940 mètres de profondeur, contenant près de 44,9 milliards de mètres cubes de gaz, dont 78 %, soit 35 milliards de mètres cubes, sont exploitables. Il est alors classé dans la catégorie des gisements majeurs(1).
De par sa composition, son gaz est dit humide(4), c’est-à-dire qu’il contient une forte proportion d’hydrocarbures plus lourds que le méthane. De plus, il présente une faible part d’impuretés, représentée par le CO₂, l’azote et le H₂S. Sa production maximale, de 4,62 millions de m³/jour, a été maintenue pendant cinq ans (1974-1979), avec un maximum de 19 puits actifs. Le dernier puits a été fermé en 2007, et le gisement est aujourd’hui complètement épuisé.
Information générale :
- Découverte : 1959
- Mise en production : 1960
- Type : Conventionnel Onshore Majeur(1)
- Profondeur : 880 m
- Distance à forer : 880 m
- Réserve en place : 53,8 milliards de m3
- Taux de récupération : 78 %
- Réserve récupérable : 42 milliards de m3
- Réserve déjà produite : 42 milliards de m3
- Réserve extractible restante : 0 milliards de m3
- Production journalière maximale enregistrée : 5,54 millions de m3 par jour
- Temps durant lequel cette production a été maintenue : 6 ans, de 1973 à 1979
- Nombre de puits maximum enregistré en activité : 23
- Nombre de puits en activité : 0
- Production moyenne par puits en activité : 0 m³ par jour
- Production actuelle : 0 m³ par jour
- Fermeture du dernier puits : 2009
Composition du gaz :
- Méthane : 81 %
- Éthane : 3 %
- Propane : 1 %
- Butane : 0,5 %
- Dioxyde de carbone : 0,5 %
- Azote : 10 %
- Sulfure d’hydrogène : 2 %
- Hélium : 2%
Le champ gazier Solaris, découvert en 1959 et mis en production en 1960, est le troisième gisement découvert sur le sol raskenois. Il s’agit d’un gisement onshore situé à 880 mètres de profondeur, contenant près de 44,9 milliards de mètres cubes de gaz, dont 78 %, soit 35 milliards de mètres cubes, sont exploitables. Il est alors classé dans la catégorie des gisements majeurs(1).
De par sa composition, son gaz est dit modérément acide(5), à forte teneur en azote(8) et à haute teneur en hélium(9), c’est-à-dire qu’il contient une forte proportion de sulfure d’hydrogène, d’azote et d’hélium. Sa forte teneur en hélium rend son extraction économiquement intéressante. Sa production maximale, de 5,64 millions de m³/jour, a été maintenue pendant six ans (1973-1979), avec un maximum de 19 puits actifs. Le dernier puits a été fermé en 2009, et le gisement est aujourd’hui complètement épuisé.
Information générale :
- Découverte : 1970
- Mise en production : 1971
- Type : Conventionnel Onshore Majeur(1)
- Profondeur : 1100 m
- Distance à forer : 1200 m
- Réserve en place : 97,5 milliards de m3
- Taux de récupération : 82 %
- Réserve récupérable : 80 milliards de m3
- Réserve déjà produite : 79,72 milliards de m3
- Réserve extractible restante : 0,28 milliards de m³
- Production journalière maximale enregistrée : 10,56 millions de m3 par jour
- Temps durant lequel cette production a été maintenue : 6 ans, de 1985 à 1991
- Nombre de puits maximum enregistré en activité : 40
- Nombre de puits en activité : 10
- Production moyenne par puits en activité : 62 100m3 par jour
- Production actuelle : 0,62 millions de m³ par jour
- Fermeture du dernier puits : 2017
Composition du gaz :
- Méthane : 90 %
- Éthane : 2 %
- Propane : 2 %
- Butane : 1 %
- Dioxyde de carbone : 0,5 %
- Azote : 1 %
- Sulfure d’hydrogène : 3 %
- Hélium : 0%
Le champ gazier Caelum, découvert en 1970 et mis en production en 1971, est le quatrième gisement découvert sur le sol raskenois. Il s’agit d’un gisement onshore situé à 880 mètres de profondeur, contenant près de 44,9 milliards de mètres cubes de gaz, dont 78 %, soit 35 milliards de mètres cubes, sont exploitables. Il est alors classé dans la catégorie des gisements majeurs(1).
De par sa composition, son gaz est dit modérément acide(5), c’est-à-dire qu’il contient une forte proportion de sulfure d’hydrogène. En dehors du H₂S, son gaz est relativement pur, contenant environ 96 % de combustible en proportion. Sa production maximale, de 10,56 millions de m³/jour, a été maintenue pendant six ans (1985-1991), avec un maximum de 40 puits actifs. Le dernier puits devrait être fermé en 2017, et le gisement est aujourd’hui quasiment épuisé.
Information générale :
- Découverte : 1976
- Mise en production : 1977
- Type : Conventionnel Offshore Géant(2)
- Profondeur : 1200 m
- Distance à forer : 1100 m
- Réserve en place : 179 milliards de m3
- Taux de récupération : 67 %
- Réserve récupérable : 120 milliards de m3
- Réserve déjà produite : 91 milliards de m3
- Réserve extractible restante : 29 milliards de m³
- Production journalière maximale enregistrée : 13 millions de m3 par jour
- Temps durant lequel cette production a été maintenue : 6 ans, de 1998 à 2006
- Nombre de puits maximum enregistré en activité : 56
- Nombre de puits en activité : 35
- Production moyenne par puits en activité : 234 000m3 par jour
- Production actuelle : 8,19 millions de m³ par jour
- Fermeture du dernier puits : 2037
Composition du gaz :
- Méthane : 75 %
- Éthane : 5 %
- Propane : 2 %
- Butane : 1 %
- Dioxyde de carbone : 5 %
- Azote : 3 %
- Sulfure d’hydrogène : 8 %
- Hélium : 1 %
Le champ gazier Astralix, découvert en 1976 et mis en production en 1977, est le cinquième gisement découvert sur le sol raskenois. Il s’agit d’un gisement offshore situé à 1 500 mètres de profondeur, contenant près de 179 milliards de mètres cubes de gaz, dont 67 %, soit 120 milliards de mètres cubes, sont exploitables. Il est alors classé dans la catégorie des gisements géants(2).
De par sa composition, son gaz est dit acide(6), modérément enrichi en azote(7) et à haute teneur en hélium(9), c’est-à-dire qu’il contient une forte proportion de sulfure d’hydrogène. Sa production maximale, de 10,56 millions de m³/jour, a été maintenue pendant huit ans (1998-2006), avec un maximum de 40 puits actifs. Le dernier puits devrait être fermé en 2017, et le gisement est aujourd’hui quasiment épuisé.
Information générale :
- Découverte : 1986
- Mise en production : 1987
- Type : Conventionnel Offshore Géant(2)
- Profondeur : 1400 m
- Distance à forer : 1200 m
- Réserve en place : 195 milliards de m3
- Taux de récupération : 68 %
- Réserve récupérable : 133 milliards de m3
- Réserve déjà produite : 44,7 milliards de m3
- Réserve extractible restante : 88,3 milliards de m³
- Production journalière maximale enregistrée : 7,5 millions de m3 par jour
- Temps durant lequel cette production a été maintenue : 21 ans, de 2002 à 2023
- Nombre de puits maximum enregistré en activité : 28
- Nombre de puits en activité : 28
- Production moyenne par puits en activité : 267 857m3 par jour
- Production actuelle : 7,5 millions de m³ par jour
- Fermeture du dernier puits : 2075
Composition du gaz :
- Méthane : 72 %
- Éthane : 5 %
- Propane : 2 %
- Butane : 1 %
- Dioxyde de carbone : 8 %
- Azote : 2 %
- Sulfure d’hydrogène : 9 %
- Hélium : 1 %
Le champ gazier Heliosphere, découvert en 1986 et mis en production en 1987, est le sixième gisement découvert sur le sol raskenois. Il s’agit d’un gisement offshore situé à 1 400 mètres de profondeur, contenant près de 195 milliards de mètres cubes de gaz, dont 68 %, soit 133 milliards de mètres cubes, sont exploitables. Il est alors classé dans la catégorie des gisements géants(2).
De par sa composition, son gaz est dit acide(6) et à haute teneur en hélium(9), c’est-à-dire qu’il contient une forte proportion de sulfure d’hydrogène et d’hélium. Sa production maximale, de 7,5 millions de m³/jour, sera maintenue pendant 21 ans (2002-2023), avec un maximum de 28 puits actifs. Le dernier puits devrait être fermé en 2075, et le gisement est aujourd’hui en pleine exploitation, c’est-à-dire que la moitié de ses réserves n’a pas encore été consommée.
Information générale :
- Découverte : 1986
- Mise en production : 1987
- Type : Conventionnel Offshore Majeur(2)
- Profondeur : 1400 m
- Distance à forer : 1600 m
- Réserve en place : 46,5 milliards de m3
- Taux de récupération : 86 %
- Réserve récupérable : 40 milliards de m3
- Réserve déjà produite : 24,9 milliards de m3
- Réserve extractible restante : 15,1 milliards de m³
- Production journalière maximale enregistrée : 5,28 millions de m3 par jour
- Temps durant lequel cette production a été maintenue : 6 ans, de 2005 à 2011
- Nombre de puits maximum enregistré en activité : 24
- Nombre de puits en activité : 19
- Production moyenne par puits en activité : 226 347m3 par jour
- Production actuelle : 4,3 millions de m³ par jour
- Fermeture du dernier puits : 2049
Composition du gaz :
- Méthane : 98 %
- Éthane : 1,5 %
- Propane : 0,3 %
- Butane : 0,1 %
- Dioxyde de carbone : 0,1 %
- Azote : 0,1 %
- Sulfure d’hydrogène : 0 %
- Hélium : 0 %
Le champ gazier Cosmodôme, Découvert en 1986 et mis en production en 1987, est le septième gisement découvert sur le sol raskenois. Il s’agit d’un gisement onshore situé à 1 400 mètres de profondeur, contenant près de 46,5 milliards de mètres cubes de gaz, dont 86 %, soit 40 milliards de mètres cubes, sont exploitables. Il est alors classé dans la catégorie des gisements majeurs(1).
De par sa composition, son gaz est dit sec(3), c’est-à-dire qu’il contient une très forte proportion de combustible. Sa production maximale, de 5,28 millions de m³/jour, a été maintenue pendant six ans (2005-2011), avec un maximum de 24 puits actifs. Le dernier puits devrait être fermé en 2049, et le gisement est aujourd’hui dans sa seconde phase d’exploitation, c’est-à-dire que plus de la moitié de ses réserves a déjà été consommée.
Gaz associé super géant plateau de Crystal
Le gaz associé est, à contrario des gisements précédents, du gaz associé, comme son nom l’indique, au pétrole, c’est-à-dire que le gaz est présent dans le pétrole et remonte avec lui lors de son exploitation. Généralement, il est soit réinjecté dans le gisement pour maintenir la pression, soit brûlé en torchère si l’on ne peut rien en faire. Cependant, grâce au vaste plan de capture et de séquestration de carbone mis en place dans le pays, nous serons bientôt en capacité d’injecter de grandes quantités de CO₂ dans ces gisements, ce qui nous permettra d’en extraire le gaz sans compromettre la récupération du pétrole en faisant baisser la pression. Les super-géants du plateau de Crystal sont au nombre de six et contiennent, d’après nos estimations, près de 980 milliards de mètres cubes de gaz, soit plusieurs fois plus que nos réserves historiques.
Information générale :
- Découverte : 2010
- Mise en production : 2016
- Type : Gaz associé
- Profondeur : 10700 m
- Distance à forer : 10700 m
- Réserve en place : 219 milliards de m3
- Taux de récupération : 95 %
- Réserve récupérable : 208 milliards de m3
- Réserve déjà produite : 0 milliards de m3
- Réserve extractible restante : 208 milliards de m³
- Production journalière maximale prévu : 22 millions de m3 par jour
- Temps durant lequel cette production a devrait être maintenue : 11 ans, de 2022 à 2033
- Nombre de puits maximum enregistré en activité : 157 (le gaz remonte par les même puits de production que le pétrole
- Nombre de puits en activité : 157 (le gaz est pour l’instant réinjecté)
- Production moyenne par puits en activité : 0m3 par jour
- Production actuelle : 0 millions de m³ par jour
- Fermeture du dernier puits : 2094
Composition du gaz :
- Méthane : 45 %
- Éthane : 20 %
- Propane : 12 %
- Butane : 5 %
- Pentane et plus lourd : 5 %
- Dioxyde de carbone : 5 %
- Azote : 0 %
- Sulfure d’hydrogène : 2 %
- Hélium : 0 %
Information générale :
- Découverte : 2010
- Mise en production : 2016
- Type : Gaz associé
- Profondeur : 9200 m
- Distance à forer : 9200 m
- Réserve en place : 200 milliards de m3
- Taux de récupération : 93 %
- Réserve récupérable : 186 milliards de m3
- Réserve déjà produite : 0 milliards de m3
- Réserve extractible restante : 186 milliards de m³
- Production journalière maximale prévu : 18 millions de m3 par jour
- Temps durant lequel cette production devrait être maintenue : 12 ans, de 2022 à 2034
- Nombre de puits maximum enregistré en activité : 120 (le gaz remonte par les même puits de production que le pétrole
- Nombre de puits en activité : 120 (le gaz est pour l’instant réinjecté)
- Production moyenne par puits en activité : 0m3 par jour
- Production actuelle : 0 millions de m³ par jour
- Fermeture du dernier puits : 2090
Composition du gaz :
- Méthane : 70 %
- Éthane : 12 %
- Propane : 8 %
- Butane : 3 %
- Pentane et plus lourd : 3 %
- Dioxyde de carbone : 2 %
- Azote : 2 %
- Sulfure d’hydrogène : 0 %
- Hélium : 0 %
Information générale :
- Découverte : 2010
- Mise en production : 2016
- Type : Gaz associé
- Profondeur : 9400 m
- Distance à forer : 9400 m
- Réserve en place : 182,6 milliards de m3
- Taux de récupération : 98 %
- Réserve récupérable : 179 milliards de m3
- Réserve déjà produite : 0 milliards de m3
- Réserve extractible restante : 179 milliards de m³
- Production journalière maximale prévu : 14 millions de m3 par jour
- Temps durant lequel cette production a devrait être maintenue : 16 ans, de 2021 à 2037
- Nombre de puits maximum enregistré en activité : 118 (le gaz remonte par les même puits de production que le pétrole
- Nombre de puits en activité : 118 (le gaz est pour l’instant réinjecté)
- Production moyenne par puits en activité : 0m3 par jour
- Production actuelle : 0 millions de m³ par jour
- Fermeture du dernier puits : 2109
Composition du gaz :
- Méthane : 55 %
- Éthane : 18 %
- Propane : 10 %
- Butane : 6 %
- Pentane et plus lourd : 7 %
- Dioxyde de carbone : 2 %
- Azote : 0 %
- Sulfure d’hydrogène : 2 %
- Hélium : 0 %
Information générale :
- Découverte : 2010
- Mise en production : 2028
- Type : Gaz associé
- Profondeur : 10100 m
- Distance à forer : 10100 m
- Réserve en place : 171,1 milliards de m3
- Taux de récupération : 97 %
- Réserve récupérable : 166 milliards de m3
- Réserve déjà produite : 0 milliards de m3
- Réserve extractible restante : 166 milliards de m³
- Production journalière maximale prévu : 21,4 millions de m3 par jour
- Temps durant lequel cette production a devrait être maintenue : 1 ans, de 2060
- Nombre de puits maximum enregistré en activité : 126 (le gaz remonte par les même puits de production que le pétrole
- Nombre de puits en activité : 126 (le gaz est pour l’instant réinjecté)
- Production moyenne par puits en activité : 0m3 par jour
- Production actuelle : 0 millions de m³ par jour
- Fermeture du dernier puits : 2103
Composition du gaz :
- Méthane : 50 %
- Éthane : 20 %
- Propane : 10 %
- Butane : 5 %
- Pentane et plus lourd : 7 %
- Dioxyde de carbone : 5 %
- Azote : 0 %
- Sulfure d’hydrogène : 2 %
- Hélium : 0 %
Information générale :
- Découverte : 2010
- Mise en production : 2028
- Type : Gaz associé
- Profondeur : 9700 m
- Distance à forer : 9700 m
- Réserve en place : 162,1 milliards de m3
- Taux de récupération : 95 %
- Réserve récupérable : 154 milliards de m3
- Réserve déjà produite : 0 milliards de m3
- Réserve extractible restante : 154 milliards de m³
- Production journalière maximale prévu : 19,47 millions de m3 par jour
- Temps durant lequel cette production a devrait être maintenue : 1 ans, de 2059
- Nombre de puits maximum enregistré en activité : 132 (le gaz remonte par les même puits de production que le pétrole
- Nombre de puits en activité : 132 (le gaz est pour l’instant réinjecté)
- Production moyenne par puits en activité : 0m3 par jour
- Production actuelle : 0 millions de m³ par jour
- Fermeture du dernier puits : 2108
Composition du gaz :
- Méthane : 75 %
- Éthane : 10 %
- Propane : 6 %
- Butane : 3 %
- Pentane et plus lourd : 2 %
- Dioxyde de carbone : 2 %
- Azote : 2 %
- Sulfure d’hydrogène : 0 %
- Hélium : 0 %
Information générale :
- Découverte : 2010
- Mise en production : 2028
- Type : Gaz associé
- Profondeur : 9200 m
- Distance à forer : 9200 m
- Réserve en place : 96,6 milliards de m3
- Taux de récupération : 90 %
- Réserve récupérable : 87 milliards de m3
- Réserve déjà produite : 0 milliards de m3
- Réserve extractible restante : 87 milliards de m³
- Production journalière maximale prévu : 12,1 millions de m3 par jour
- Temps durant lequel cette production a devrait être maintenue : 1 ans, de 2054
- Nombre de puits maximum enregistré en activité : 80 (le gaz remonte par les même puits de production que le pétrole
- Nombre de puits en activité : 80 (le gaz est pour l’instant réinjecté)
- Production moyenne par puits en activité : 0m3 par jour
- Production actuelle : 0 millions de m³ par jour
- Fermeture du dernier puits : 2109
Composition du gaz :
- Méthane : 60 %
- Éthane : 15 %
- Propane : 8 %
- Butane : 5 %
- Pentane et plus lourd : 6 %
- Dioxyde de carbone : 4 %
- Azote : 0 %
- Sulfure d’hydrogène : 2 %
- Hélium : 0 %
Gaz de charbon (non-conventionnel)
Le gaz de charbon, aussi nommé Coal Bed Methane (CBM), est le gaz contenu dans les pores du charbon, connu sous le nom de grisou, responsable de nombreux accidents dans les mines de charbon souterraines. Même épuisée, une mine de charbon contient toujours du charbon, on dit que ce charbon est inexploitable, du moins pas de manière rentable, que ce soit économiquement ou énergétiquement. Ainsi, on estime qu’en moyenne, le rapport entre charbon exploitable et inexploitable est de 1 pour 17. Cela veut donc dire que, par exemple, Rasken, qui disposait à l’origine de 11,4 milliards de tonnes de charbon exploitable, a en fait sous ses pieds 198.9 milliards de tonnes de charbon inexploitable. Ce qui fait que, même si le charbon Raskenois n’est pas très méthanogène, c’est-à-dire qu’il ne contient pas beaucoup de méthane, les quantités deviennent très vite importantes. En effet, la quantité de méthane contenue dans le charbon varie en fonction du type de charbon. On a donc, par exemple, 7 mètres cubes de méthane par tonne d’anthracite, alors que les charbons de moins bonne qualité, comme la lignite, en contiennent environ 25. Aussi, il ne faut pas seulement prendre en compte le type de charbon, mais également la profondeur, car plus il est profondément enfoui, plus grande est sa capacité à stocker du méthane. Ainsi, un charbon bitumineux à 500 mètres de profondeur ne stocke que 15 mètres cubes, alors que le même charbon à 1500 mètres peut stocker 40 mètres cubes. Malheureusement pour nous, la majorité du charbon Raskenois est de l’anthracite à faible profondeur (93,8 %), le reste étant du charbon bitumineux.
Cependant, tout n’est pas rose. Bien que d’énormes quantités de gaz soient contenues dans le charbon, la perméabilité de celui-ci empêche de produire une grande partie du gaz. Ainsi, si l’on exploite juste le gaz en forant un trou simple, le taux de récupération pour de l’anthracite est compris entre 10 et 30 %. Un moyen d’augmenter cela est de fracturer le charbon, soit avec de l’eau, soit avec de l’air comprimé. Cela permet d’augmenter la perméabilité de la roche et donc de faciliter le passage du gaz. Un autre moyen d’augmenter le taux de récupération est de forcer le gaz à se diriger vers les puits de production. Cela se fait majoritairement par injection de CO2, car ce gaz a une meilleure affinité que le méthane pour le charbon. Enfin, il faut prendre en compte que ce type de gisement de gaz a une faible production par puits. En effet, pour ce type de gisement, on peut produire en moyenne 15 000 mètres cubes par puits, alors que, sur un gisement standard, cela peut monter à plus d’un million.
Information générale :
- Découverte : 1854
- Mise en production : 2016
- Type : Gaz de charbon
- Profondeur : 150 m
- Distance à forer : 150 m
- Type de charbon : Anthracite
- Teneur en méthane : 7m3/Tonnes
- Réserve en place : 336 milliards de m3
- Taux de récupération : 45 %
- Réserve récupérable : 151,2 milliards de m3
- Réserve déjà produite : 0 milliards de m3
- Réserve extractible restante : 151,2 milliards de m³
- Production journalière maximale prévu : 9 millions de m3 par jour
- Temps durant lequel cette production a devrait être maintenue : 21 ans, de 2020 à 2041
- Nombre de puits maximum enregistré en activité : 0
- Nombre de puits maximum en activité prévu : 600
- Production moyenne par puits en activité prévu : 15 000m3 par jour
- Production actuelle : 0 millions de m³ par jour
- Fermeture du dernier puits : 2083
Injection de CO2 :
- Nombre de puits d’injection : 22
- Injection moyenne par puits en activité prévu : 491 tonnes par jours
- Quantité de CO2 injecté prévu : 10 800 tonnes par jours
- Quantité totale de CO2 injecté sur la durée de vie du gisement : 264 millions de tonnes
Composition du gaz :
- Méthane : 92 %
- Dioxyde de carbone : 5 %
- Azote : 2 %
- Sulfure d’hydrogène : 1 %
Information générale :
- Découverte : 1864
- Mise en production : 2016
- Type : Gaz de charbon
- Profondeur : 180 m
- Distance à forer : 180 m
- Type de charbon : Anthracite
- Teneur en méthane : 8m3/Tonnes
- Réserve en place : 489,6 milliards de m3
- Taux de récupération : 42 %
- Réserve récupérable : 205,6 milliards de m3
- Réserve déjà produite : 0 milliards de m3
- Réserve extractible restante : 205,6 milliards de m³
- Production journalière maximale prévu : 10 millions de m3 par jour
- Temps durant lequel cette production a devrait être maintenue : 24 ans, de 2022 à 2046
- Nombre de puits maximum enregistré en activité : 0
- Nombre de puits maximum en activité prévu : 715
- Production moyenne par puits en activité prévu : 14 000m3 par jour
- Production actuelle : 0 millions de m³ par jour
- Fermeture du dernier puits : 2113
Injection de CO2 :
- Nombre de puits d’injection : 24
- Injection moyenne par puits en activité prévu : 500 tonnes par jours
- Quantité de CO2 injecté prévu : 12 000 tonnes par jours
- Quantité totale de CO2 injecté sur la durée de vie du gisement : 424,8 millions de tonnes
Composition du gaz :
- Méthane : 88 %
- Dioxyde de carbone : 7 %
- Azote : 4 %
- Sulfure d’hydrogène : 1 %
Information générale :
- Découverte : 1940
- Mise en production : 2025
- Type : Gaz de charbon
- Profondeur : 1200 m
- Distance à forer : 1200 m
- Type de charbon : Anthracite
- Teneur en méthane : 6m3/Tonnes
- Réserve en place : 134,4 milliards de m3
- Taux de récupération : 50 %
- Réserve récupérable : 67,2 milliards de m3
- Réserve déjà produite : 0 milliards de m3
- Réserve extractible restante : 67,2 milliards de m³
- Production journalière maximale prévu : 4 millions de m3 par jour
- Temps durant lequel cette production a devrait être maintenue : 22 ans, de 2028 à 2050
- Nombre de puits maximum enregistré en activité : 0
- Nombre de puits maximum en activité prévu : 223
- Production moyenne par puits en activité prévu : 18 000m3 par jour
- Production actuelle : 0 millions de m³ par jour
- Fermeture du dernier puits : 2112
Injection de CO2 :
- Nombre de puits d’injection : 10
- Injection moyenne par puits en activité prévu : 480 tonnes par jours
- Quantité de CO2 injecté prévu : 4 800 tonnes par jours
- Quantité totale de CO2 injecté sur la durée de vie du gisement : 152,4 millions de tonnes
Composition du gaz :
- Méthane : 80 %
- Dioxyde de carbone : 10 %
- Azote : 8 %
- Sulfure d’hydrogène : 2 %
Information générale :
- Découverte : 1970
- Mise en production : 2025
- Type : Gaz de charbon
- Profondeur : 1500 m
- Distance à forer : 1500 m
- Type de charbon : Charbon bitumineux
- Teneur en méthane : 35m3/Tonnes
- Réserve en place : 367,5 milliards de m3
- Taux de récupération : 65 %
- Réserve récupérable : 238,87 milliards de m3
- Réserve déjà produite : 0 milliards de m3
- Réserve extractible restante : 238,87 milliards de m³
- Production journalière maximale prévu : 13 millions de m3 par jour
- Temps durant lequel cette production a devrait être maintenue : 22 ans, de 2031 à 2053
- Nombre de puits maximum enregistré en activité : 0
- Nombre de puits maximum en activité prévu : 590
- Production moyenne par puits en activité prévu : 22 000m3 par jour
- Production actuelle : 0 millions de m³ par jour
- Fermeture du dernier puits : 2119
Injection de CO2 :
- Nombre de puits d’injection : 32
- Injection moyenne par puits en activité prévu : 487,5 tonnes par jours
- Quantité de CO2 injecté prévu : 15 600 tonnes par jours
- Quantité totale de CO2 injecté sur la durée de vie du gisement : 535,2 millions de tonnes
Composition du gaz :
- Méthane : 85 %
- Dioxyde de carbone : 8 %
- Azote : 6 %
- Sulfure d’hydrogène : 1 %
Définition :1-Gisement majeur : Gisement contenant entre 10 et 85 milliards de m³ exploitables
2-Gisement géant : Gisement contenant entre 85 et 850 milliards de m³ exploitables
3-Gaz sec : Gaz contenant au moins 95 % de méthane
4-Gaz humide : Gaz contenant moins de 95 % de méthane et contenant des hydrocarbure plus lourd comme l’éthane, le propane ou le butane en quantité significative.
5-Gaz modérément acide : Gaz contenant du sulfure d’hydrogène dans des proportion comprise entre 1 et 5%
6-Gaz acide : Gaz contenant du sulfure d’hydrogène dans des proportion comprise entre 5 et 15%
7-Gaz modérément enrichi en azote : Gaz contenant de l’azote dans des proportion comprise entre 3 et 10%
8-Gaz à haute teneur en azote : Gaz contenant de l’azote dans des proportion comprise entre 10 et 20%
9-Gaz à haute teneur en hélium : Gaz contenant de l’hélium dans des proportion comprise entre 1 et 3%
Pôles de traitement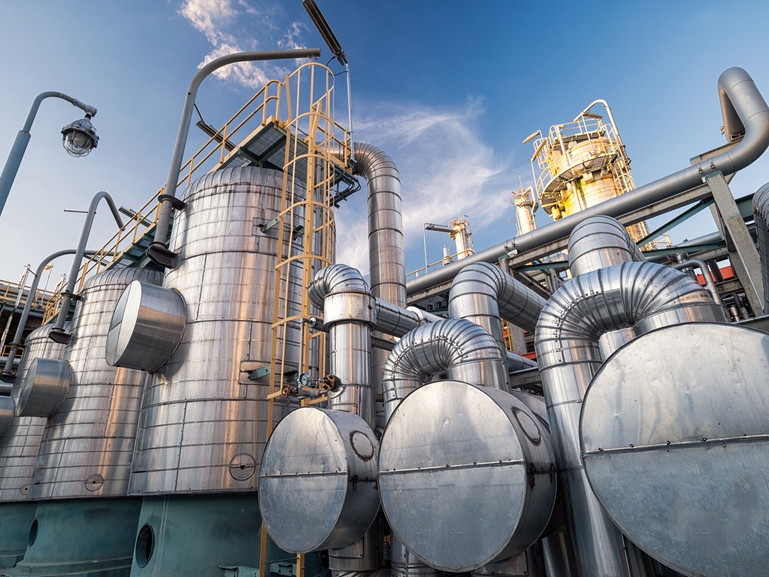
De par sa nature, le gaz est généralement traité directement sur le lieu de production du gaz brut, car, en fonction de ses impuretés, le transporter sur plusieurs kilomètres nécessiterait des gazoducs spéciaux pouvant supporter la corrosion ou d’autres phénomènes. Ainsi, à Rasken, chaque gisement dispose de son unité de traitement, y compris les deux gisements offshore que sont Astralix et Heliosphere, qui disposent de plateformes avec des extensions pour accueillir les unités de traitement.
Au total, en 2015, la production raskenoise de gaz brut s’élève à 26,5 millions de m³. En comparaison, la production de gaz naturel, donc de méthane, n’a été que de 20,7 millions de m³. Cela signifie donc que quasiment 6 millions de m³ ne sont pas du méthane. Le rôle des unités de traitement est justement de retirer cette fraction, soit pour en extraire les impuretés, soit pour procéder à un triage. Par exemple, le butane et le propane étant vendus en bouteille, alors que le méthane est vendu soit par gazoduc si vous avez un raccordement, soit un camion vient remplir votre citerne.
Au final, qu’en est-il des impuretés ?
Production gisement historiqueProduction gaz associéProduction gaz de charbonOn distingue donc deux situations similaires et une à part, en fonction des trois types de gisements. Nous allons commencer par les deux situations similaires.
Le gaz historique et le gaz associé sont deux types de gaz brut relativement similaires de par leurs composants. Ce qui change, c’est leur composition. Là où, dans nos gisements historiques, les autres gaz sont dominés par le sulfure d’hydrogène, notamment à cause de nos deux gisements offshore contenant une grande proportion de ce gaz, le gaz associé, lui, est dominé par les gaz combustibles comme l’éthane, le propane, le butane, le pentane et d’autres.
Le gaz de charbon, lui, ne contient pas d’hydrocarbures plus lourds que le méthane. Ainsi, les autres gaz présents lors de l’exploitation du gisement sont plus limités. On y trouve uniquement de l’azote, du CO₂ et du sulfure d’hydrogène.
Au final, si l’on agrège tous les types de gisements, on obtient ceci :
Nous allons donc détailler les productions des différents gaz, ainsi que leur utilité une fois séparés du reste. En premier lieu, nous allons détailler les gaz combustibles, puis les gaz valorisables, et enfin les déchets. Les valeurs seront prises pour l’année 2015.
Gaz combustiblesEn premier, on retrouve donc le trio éthane, propane/butane et pentane
- L’éthane a une production journalière en 2015 de 1,15 million de m³ par jour. Celui-ci est principalement utilisé comme matière première dans l’industrie, notamment dans la production d’éthylène, qui sert ensuite à la fabrication de matières plastiques. Il est également utilisé, dans une moindre mesure, dans l’industrie pharmaceutique et chimique pour fabriquer des solvants, des médicaments et comme stérilisant pour la médecine. Enfin, il est utilisé comme réfrigérant, notamment dans les méthaniers, grâce à sa capacité à rester liquide à basse température (-88°C).
- Ensuite viennent le propane et le butane, qui ont respectivement une production en 2015 de 0,226 et 0,456 million de m³ par jour. Ils sont principalement utilisés comme combustibles pour les gazinières ainsi que comme carburants dans le transport sous la forme de Gaz de Pétrole Liquéfié (GPL). Ils peuvent également, dans une moindre mesure, être utilisés comme gaz réfrigérant, comme gaz propulseur dans les aérosols, ainsi que dans l’industrie chimique pour la fabrication de solvants ou de plastiques.
- Vient ensuite le pentane, qui, bien qu’il ne soit pas encore produit à l’heure actuelle, le sera l’année prochaine avec la mise en production des champs du plateau de Crystal. Celui-ci est principalement utilisé comme solvant industriel, notamment pour extraire les huiles essentielles, nettoyer les composants électroniques sensibles ou encore dans l’industrie pétrolière pour le craquage du pétrole brut et la purification des hydrocarbures. Sa deuxième utilisation majeure est dans la fabrication de mousses plastiques, comme le polystyrène expansé, en remplacement des agents expansifs comme les SFS. Enfin, on le retrouve également comme fluide frigorifique dans les réfrigérateurs et climatiseurs. Le pentane, tout comme l’éthane, bien qu’étant un combustible, est très peu utilisé à cette fin.
Gaz valorisable
- L’hélium a une production de 0,213 million de m³. Ce gaz est vital pour notre société moderne, car il est présent dans des endroits insoupçonnés. On le retrouve notamment comme refroidissant dans les IRM et équipements cryogéniques. Il est également utilisé dans la fabrication de composants électroniques et de semi-conducteurs, afin d’empêcher une surchauffe. On le retrouve aussi dans le secteur aérospatial, où il sert à purger et pressuriser les réservoirs d’oxygène liquide et d’hydrogène liquide des fusées.
- Le sulfure d’hydrogène a une production en 2015 de 1,84 million de m³ par jour. À Rasken, nous avons décidé de le valoriser en séparant l’hydrogène du soufre grâce à un procédé électrochimique. Le soufre est vendu sous forme de soufre élémentaire sur le marché national et international. De même, l’hydrogène peut être valorisé dans différents secteurs.
- L’azote, avec une production de 0,548 million de m³ par jour, est généralement considéré comme un déchet dans la majorité des pays du monde. Il est soit relâché dans l’atmosphère, soit réinjecté dans le gisement. Cependant, à Rasken, nous faisons les choses différemment. Grâce à une législation avantageuse, ce gaz est entièrement valorisé. Il est majoritairement vendu à l’industrie pour la fabrication d’engrais azotés et est également utilisé comme fluide frigorifique.
Gaz non valorisables (Déchets)- Enfin, nous avons le CO₂, le seul véritable déchet avec lequel nous ne pouvons rien faire. Contrairement aux autres gaz, aucune valorisation n’est possible. Il est simplement réinjecté dans le gisement.
Pôles de transport, stockage et d’importation[img=]Apex[/img]Malgré son histoire plus récente que celle du pétrole, le réseau gazier raskenois est extrêmement développé, bien plus que celui du pétrole, la raison étant que le gaz est beaucoup plus utilisé de manière domestique. C’est-à-dire que les habitations ou n’importe quel bâtiment peuvent être raccordés au gaz, alors que ce n’est pas le cas pour le pétrole. Ainsi, en 2015, le réseau s’étendait sur 18 000 km. De plus, il a gagné depuis 2011 environ 3 000 km, du fait de la découverte des super-géants du plateau de Crystal.
En effet, dès leur découverte, il était envisagé d’exploiter un jour leur gaz associé. C’est en prévision de cela que de nombreuses connexions furent établies entre les super-géants et le reste du réseau. De plus, il devrait encore gagner environ 2 000 km dans les années à venir avec la mise en production du gaz contenu dans les gisements de charbon. Ainsi, à terme, le réseau devrait s’étendre sur 20 000 km à l’horizon 2020 et ne devrait plus grandir de manière significative à partir de là. Les années post-2020 se concentreront uniquement sur l’exploitation et l’entretien du réseau ainsi que sur son adaptation à la part croissante de biogaz.
Afin de garantir une sécurité énergétique, et du fait de sa forte consommation de gaz pour sa production électrique, Rasken dispose de réserves de gaz conséquentes. Au total, ce ne sont pas moins de 15 dépôts pouvant stocker près de 20 milliards de m³ de gaz, répartis sur le territoire raskenois. Sur le territoire national, il existe deux types de dépôts différents :
Les cavités salines : Ces cavités sont formées artificiellement par l’injection d’eau dans une formation saline afin de dissoudre le sel. Une fois le sel dissous, l’eau salée est pompée, ce qui crée une cavité vide et étanche, prête à être mise sous pression par l’injection de gaz. Ce type de stockage est le plus répandu avec 15 sites, cependant, il ne représente que 5 milliards de m³ de stockage. Malgré sa capacité de stockage plus faible, l’avantage des cavités salines est qu’elles permettent des cycles d’injection et de soutirage plus rapides, idéales pour répondre aux variations rapides de la demande. Les aquifères : Il s’agit de formations de roches poreuses gorgées d’eau. Ce type de stockage a pour avantage d’offrir des volumes importants, adaptés à une modulation saisonnière, donc plus lente que celle des cavités salines.Du fait de sa dépendance aux importations de gaz, Rasken a dû très tôt construire des moyens d’importation afin de pallier ce manque de production. En effet, dès 1988, il n’y avait plus aucun doute que Rasken allait perdre son indépendance gazière. Ainsi, cette année-là, la construction du premier terminal méthanier du pays, dans la ville de Lengenbruck, débuta et était prévue pour durer cinq ans, avec une capacité d’importation de 20 millions de m³ par jour.
Cependant, ce que l’on n’avait pas prévu, c’était que la consommation du pays augmenterait aussi vite. Ainsi, en 1991, alors que le chantier battait son plein, le pays devint, pour la première fois de son histoire, déficitaire en gaz. Le terminal étant en cours de construction, le pays dut utiliser ses réserves stratégiques pour combler le manque de production. Malheureusement, ce ne fut pas suffisant, les réserves étant trop petites, elles ne permirent de tenir qu’une seule année.
À l’époque, les réserves stratégiques de gaz ne couvraient qu’un mois de consommation, elles furent donc rapidement vidées, entraînant une crise énergétique sans précédent dans le pays. Des mesures de sobriété furent prises, mais cela marqua tout de même la décennie 1990. Pendant deux ans, le pays passa en mode sobriété le temps que le terminal soit achevé.
En 1993, ce fut chose faite, et les citoyens comme l’économie purent à nouveau respirer. Cependant, ce premier terminal méthanier n’apporta qu’un moment de répit, car si rien n’était fait, le pays serait de nouveau déficitaire en gaz dès 2001.
Ainsi, en 1995, la construction d’un deuxième terminal méthanier commença dans le port de Bonnberg, avec une capacité de 50 millions de m³ par jour. Puis, enfin, en 2005, l’extension du terminal de Lengenbruck fut lancée, portant sa capacité à 50 millions de m³ par jour, comme pour Bonnberg.
Émissions de CO2Au même titre que son homologue liquide, l’industrie du gaz naturel est une activité polluante. Cependant, là où elle se démarque du pétrole, c’est dans la quantité de CO₂ émise. En effet, comme vous pouvez le voir dans le graphique ci-dessus, les quantités émises sont incomparables à celles du pétrole. Cependant, il faut relativiser, car on ne peut pas comparer un baril de pétrole à un m³ de gaz, du moins pas directement. Si l’on veut comparer les émissions, il faut le faire avec une valeur qui ne varie pas ou peu. Cette valeur, c’est l’énergie. En effet, un baril de pétrole moyen et un m³ de gaz naturel moyen contiennent une certaine quantité d’énergie. À quantité d’énergie équivalente, le gaz naturel produit en moyenne 1,5 à 2 fois moins de CO₂ que le pétrole.
Comme pour le pétrole, les émissions de CO₂ du secteur gazier sont étroitement liées à la production même du gaz. C’est pour cela que l’on observe un premier pic d’émissions en 2002, qui correspond presque (à deux années près) au pic de production de gaz. Voici donc maintenant les émissions de CO₂ de la branche gaz naturel d’Apex. Comme pour le pétrole, les émissions sont découpées en trois pôles différents, eux-mêmes subdivisés en plusieurs secteurs.
Pole Production :Comme pour le pétrole, les sites d’extraction du gaz naturel nécessitent un ensemble de machines assurant le bon fonctionnement de l’extraction. On y retrouve donc des pompes, des compresseurs et des équipements de forage. Cependant, à la différence du pétrole, où ces machines sont alimentées par des groupes électrogènes du fait de l’isolement des gisements sur le plateau de Crystal, les gisements de gaz, eux, sont raccordés au réseau électrique. Ils bénéficient donc d’une électricité qui est certes carbonée, mais bien moins qu’elle ne le serait si elle provenait de groupes électrogènes. De plus, le mix électrique se décarbone progressivement avec le déploiement de notre parc nucléaire.Les émissions de CO₂ directement liées à l’extraction du gaz sont généralement de l’ordre de 0,01 à 0,03 kg de CO₂ par m³ de gaz extrait. Ce secteur représentait en 2015 environ 0,1 million de tonnes de CO₂.
Ensuite viennent les fuites de méthane. Pour elles, c’est simple : elles ont été complètement éradiquées dans notre pays en 2007. Cependant, en moyenne dans le monde, les émissions liées aux fuites de méthane se situent entre 0,02 et 0,07 kg de CO₂ par m³ de gaz extrait. À son pic, les fuites de méthane représentaient 0,86 million de tonnes de CO₂. On peut également citer le torchage du gaz naturel, mais cette pratique n’a jamais existé dans notre pays pour les gisements de gaz, contrairement aux gisements de pétrole.
Pole Traitement : Dans le pôle traitement, on retrouve d’abord l’électricité nécessaire au fonctionnement des installations, incluant tout ce qui concerne la circulation et la séparation des hydrocarbures. Les émissions sont typiquement de 0,01 à 0,03 kg de CO₂ par m³ de gaz traité. Cependant, ce facteur d’émission devrait chuter dans moins de 10 ans à une valeur bien plus faible, autour de 0,0033 kg de CO₂, grâce à la fermeture de nos centrales à charbon et la mise en place de la capture et séquestration du carbone sur nos centrales à gaz. En 2015, l’électricité nécessaire au fonctionnement de nos installations de traitement a été responsable de l’émission de 0,32 million de tonnes de CO₂.
Ensuite, on retrouve le traitement du H₂S (sulfure d’hydrogène), un gaz acide qui doit être traité. Généralement, celui-ci est traité par le procédé de Klaus afin d’en retirer le soufre. Cependant, à Rasken, nous utilisons un procédé électrochimique. Ce procédé, bien que plus émetteur de CO₂ que celui de Klaus (0,05 kg contre 0,01 kg de CO₂ par m³ de gaz traité), nous permet d’extraire l’hydrogène en plus du soufre afin de le valoriser. Ces deux éléments sont ensuite revendus. À Rasken, les émissions liées au traitement du sulfure d’hydrogène sont de 0,025 kg de CO₂ par m³ de gaz traité, soit 0,4 million de tonnes de CO₂ en 2015.
Comme le H₂S, d’autres gaz doivent être extraits afin de fournir aux consommateurs un produit de qualité. L’azote est présent naturellement dans un gisement de gaz, mais il est inerte, c’est-à-dire qu’il n’apporte rien et, en trop grande quantité, nuit à la capacité énergétique du gaz. Nous devons donc l’extraire par divers procédés. Une fois extrait, nous avons plusieurs options : le réinjecter dans le gisement, le relâcher dans l’air, ou encore le revendre. Il est notamment revendu aux industries qui achètent l’hydrogène pour fabriquer de l’ammoniac, utilisé ensuite dans la production d’engrais. L’extraction de l’azote du gaz représente des émissions de l’ordre de 0,03 kg de CO₂ par m³ de gaz traité, soit 0,29 million de tonnes de CO₂ en 2015.
Vient enfin le dernier gaz à séparer, le CO₂. Celui-ci est pire que l’azote, car il n’est tout simplement pas valorisable. La seule utilité possible de ce gaz est d’être réinjecté dans le gisement afin de maintenir la pression. L’extraction du CO₂ du gaz brut a un facteur d’émission de 0,041 kg de CO₂ par m³ de gaz traité, ce qui représente environ 0,4 million de tonnes de CO₂ en 2015.
Pole Transport/stockage et importation : Le transport et le stockage du gaz naturel sont également émetteurs de CO₂, en raison des nombreuses pompes nécessaires pour faire transiter le gaz. À Rasken, les émissions sont de 0,005 kg, soit 5 grammes de CO₂ par m³ de méthane. Ce facteur étant lié au gaz qui transite, il dépend directement de la consommation de gaz et non de la production. Ainsi, en 2015, les émissions dues au transport et au stockage ont été de 0,21 million de tonnes de CO₂.
Pour finir, étant donné que Rasken consomme plus de gaz qu’il n’en produit, nous devons importer une part significative de notre gaz. Ainsi, nous disposons de terminaux méthaniers, servant à accueillir les méthaniers et leurs cargaisons. Le gaz naturel arrive sous forme liquide afin d’être transporté en plus grande quantité. Pour l’injecter sur le réseau, il faut donc le regazéifier. Il existe plusieurs méthodes pour cela : par exemple, brûler du gaz naturel, mais cette technique, bien que très efficace, entraîne des émissions de CO₂ conséquentes.
À Rasken, nous avons préféré utiliser l’eau de mer pour réchauffer le méthane liquide. Cette méthode permet d’avoir des émissions très faibles, car elles proviennent uniquement des circulateurs utilisés pour faire circuler le liquide. Ainsi, le facteur d’émission est de 0,003 kg, soit 3 grammes de CO₂ par m³, soit 0,13 million de tonnes de CO₂ en 2015.
Solution pour l’avenir : En 2015, les émissions du secteur gazier d’Apex s’élevaient à 1,69 million de tonnes de CO₂. Malheureusement, nous ne pourrons guère descendre plus bas. Le cycle étant en grande partie électrifié, le seul paramètre sur lequel nous pouvons agir est l’intensité carbone de notre électricité. Malheureusement, le déploiement du nucléaire et la fermeture des centrales à charbon ne permettront pas de compenser l’augmentation des émissions due à l’accroissement de la production de gaz, avec la mise en exploitation du plateau de Crystal et du gaz de charbon. Ainsi, d’ici quelques années, les émissions de CO₂ du pôle gazier devraient monter jusqu’à 7,5 millions de tonnes.
Chiffre d'affaire
Bien que plus récent que le secteur pétrolier, l’industrie du gaz naturel possède également un poids conséquent dans l’activité de notre entreprise. Comme pour le pétrole, la découverte des super-géants du plateau de Crystal va renforcer le chiffre d’affaires du gaz naturel grâce à la mise en production du gaz associé à ces gisements. En 2015, le chiffre d’affaires du pôle gazier d’Apex Energy représente environ 7,5 milliards de Sleks (15 milliards d’euros). Cependant, avec la mise en production du gaz associé et du gaz de charbon, celui-ci devrait s’envoler puis se stabiliser autour de 41 milliards de Sleks (82 milliards d’euros) durant la prochaine décennie.
Secteur du gaz naturel : Sous l’appellation gaz naturel se cache en réalité plusieurs gaz, comme vous avez pu le voir dans la partie traitement. Cependant, dans l’imaginaire collectif, le gaz naturel correspond au gaz injecté dans le réseau, alors qu’il est composé quasiment exclusivement de méthane, qui est le composant principal du gaz extrait.
En 2015, la production journalière moyenne de gaz brut fut de 26,54 millions de m³ par jour. Cependant, après traitement, le volume de méthane n’est plus que de 20,72 millions de m³ par jour. Avec la mise en production prochaine du gaz associé et du gaz de charbon, la production devrait remonter pour atteindre un maximum de 151 millions de m³ de gaz brut en 2031, soit une production de méthane de 95,1 millions de m³.
En moyenne, un m³ de méthane est vendu aux alentours de 0,75 Sleks (1,5 euro). Cela représente un chiffre d’affaires journalier en 2015 de 15,5 millions de Sleks (31 millions d’euros). Sur l’année 2015, cela représente 5,67 milliards de Sleks (11,34 milliards d’euros).
Secteur du raffinage : Ce secteur concerne les produits valorisés après traitement du gaz brut, en excluant le méthane. Cela comprend donc tous les hydrocarbures plus lourds que le méthane, comme l’éthane, le propane, le butane et le pentane. On retrouve également le sulfure d’hydrogène, l’hélium et l’azote, le CO₂ n’étant pas valorisable, il n’est pas pris en compte.
En première position, on retrouve l’hélium avec un chiffre d’affaires en 2015 de 1,17 milliard de Sleks (2,34 milliards d’euros). Une fois vendu, l’hélium est principalement utilisé comme fluide cryogénique, servant par exemple à refroidir les aimants supraconducteurs dans les IRM.
En deuxième position, vient le butane avec un chiffre d’affaires en 2015 de 0,333 milliard de Sleks (0,666 milliard d’euros). Le butane est principalement connu comme étant le gaz de cuisine sous la forme de bouteilles métalliques servant à alimenter les gazinières. On le retrouve cependant un peu dans la pétrochimie, où il est utilisé pour la fabrication de plastique ou de solvants.
Ensuite, on retrouve le propane, se classant troisième pour le chiffre d’affaires 2015 du pôle gazier avec 144 millions de Sleks (288 millions d’euros). Comme le butane, il est principalement utilisé dans les gazinières, la seule différence étant la couleur de la bouteille métallique, qui est différente de celle du butane.
Pour la quatrième position, on retrouve le sulfure d’hydrogène, celui-ci étant séparé dans le tableau ci-dessus en hydrogène et en soufre. En 2015, la vente des sous-produits du H₂S a généré un chiffre d’affaires de 133 millions de Sleks (266 millions d’euros).
Il faut cependant différencier les deux éléments :
- L’hydrogène représente la plus grande part du chiffre d’affaires, avec 84,5 millions de Sleks (169 millions d’euros). À Rasken, l’hydrogène produit à partir du H₂S est principalement vendu aux usines de fabrication d’ammoniac, qui en font généralement de l’engrais en le faisant réagir avec de l’azote. L’hydrogène non utilisé par cette industrie est vendu à certaines aciéries partenaires pour la production d’acier bas carbone.
- De l’autre côté, nous avons donc le soufre, avec un chiffre d’affaires de 48,5 millions de Sleks (97 millions d’euros). Le soufre est principalement vendu sous forme de soufre élémentaire à des industries pharmaceutiques, des industries chimiques pour la production d’acide, ou encore comme engrais.
À la cinquième place, on retrouve l’azote extrait du gaz brut, avec un chiffre d’affaires annuel en 2015 de 50 millions de Sleks (100 millions d’euros). L’azote extrait du gaz brut est vendu en intégralité aux mêmes industries de fabrication d’engrais qui achètent l’hydrogène. Cette pratique de valorisation de tout ce qui peut l’être est due à une réglementation Raskenoise forçant Apex à le faire. Cette obligation est quasiment inexistante dans le reste du monde.
Enfin, en dernière position, on retrouve l’éthane, avec un chiffre d’affaires de 31,45 millions de Sleks (62,9 millions d’euros). Celui-ci est principalement vendu aux industries pétrochimiques, où il sert de matière première pour la fabrication de plastiques et de solvants.
DépenseComme pour le pétrole et n’importe quel secteur d’activité, le chiffre d’affaires n’est pas égal au bénéfice, car pour fonctionner, un secteur a besoin d’argent. Ce qui fait la rentabilité d’un secteur, c’est uniquement que le chiffre d’affaires soit supérieur aux dépenses. Ainsi, pour savoir si un secteur est rentable, il est nécessaire de calculer les dépenses. Pour le pôle gaz, ces dépenses s’élèvent, en 2015, à 23 milliards de Sleks (46 milliards d’euros). Ces dépenses devraient augmenter dans les années à venir à cause de la remontée de la production gazière au sein du pays, et ce, malgré la réduction des importations. Importations qui sont actuellement les dépenses pesant le plus sur ce secteur.
En première position des dépenses, on retrouve, en 2015, les importations qui pèsent pour près de 16 milliards de Sleks (32 milliards d’euros). La production raskenoise de gaz naturel étant pour l’instant en déclin et la consommation ne faisant qu’augmenter, les importations n’ont pas arrêté d’augmenter depuis 1990. Cependant, grâce à la mise en production du gaz des super-géants du plateau de Crystal, les importations devraient diminuer à partir de 2017 et baisser au maximum à 6,7 milliards de Sleks (13,2 milliards d’euros) à l’horizon 2022, avant de réaugmenter de manière modérée après.
Le deuxième secteur de dépense est, en 2015, celui de l’extraction, avec près de 6,35 milliards de Sleks (12,7 milliards d’euros). Ce secteur englobe tout ce qui concerne la maintenance du matériel et les salaires des employés. À terme, avec la remontée de la production raskenoise de gaz naturel, les dépenses liées à ce secteur devraient monter jusqu’à 35 milliards de Sleks (70 milliards d’euros) et se stabiliser à ce niveau-là pour la décennie suivante.
Le transport du gaz naturel prend la troisième place avec "seulement" 396 millions de Sleks sur l’année 2015 (792 millions d’euros). Ce chiffre n’est pas lié à la production ou à l’importation, mais à la consommation. Ainsi, il est pour ainsi dire en perpétuelle augmentation : tant que la consommation augmentera, les dépenses liées à ce secteur augmenteront.
Pour la quatrième place, c’est le stockage qui fait son apparition avec 198 millions de Sleks (396 millions d’euros) pour l’année 2015. Comme pour le transport, ce secteur n’est pas lié à la production ou à l’importation, mais à la consommation. En effet, afin de ne pas sombrer en cas de rupture d’approvisionnement, le gouvernement veut qu’en tout instant, Rasken dispose de réserves de gaz permettant de tenir 6 mois si le pays se retrouve dans un scénario où tous ses fournisseurs ne sont plus là.
Enfin, on retrouve le traitement du gaz naturel avec la séparation et le traitement des différents gaz que sont le sulfure d’hydrogène, l’hélium et l’azote, avec respectivement des dépenses de 8,35 | 7,78 | 3 millions de Sleks (16,7 | 15,56 | 6 millions d’euros) pour l’année 2015.
DéficitAu final, et à la différence du pétrole, on se rend compte que le secteur gazier raskenois est largement déficitaire. En 2015, ce n’est pas moins de 15,5 milliards de Sleks (31 milliards d’euros) de déficit qui furent enregistrés par Apex sur le gaz. Ce secteur n’étant pas autonome, son déficit doit être compensé par d’autres sources. Ainsi, ce sont majoritairement les bénéfices du pétrole qui compensent ce déficit.
Grâce à ce graphique, nous pouvons remarquer que, grâce à la remontée de la production raskenoise, le déficit du pôle gaz raskenois d’Apex devrait en partie se résorber à partir de 2017. Le déficit le plus bas enregistré devrait être atteint en 2022 avec seulement 1,87 milliard de Sleks (3,74 milliards d’euros), avant de réaugmenter de manière modérée.
Revenir au sommaire