Apex Energy - Page 2
Posté le : 05 mars 2025 à 22:19:00
33
Posté le : 05 mars 2025 à 22:19:57
29315
Électricité
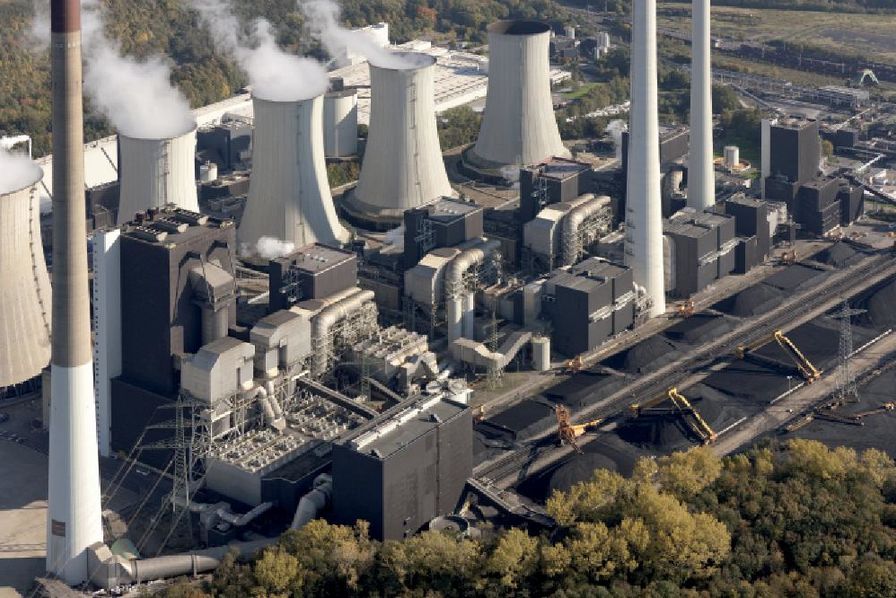
Tout au long de leur histoire, les centrales à charbon ont utilisé différentes technologies afin d’être toujours plus performantes. Sur le territoire Raskenois, il y a eu trois types de centrales, deux encore d’actualité et une abandonnée en 1980. Ces trois technologies sont les centrales dites sous-critiques, les centrales supercritiques et les centrales ultra-supercritiques. Nous allons présenter ces trois technologies par ordre d’ancienneté.
Centrale sous critique : La première technologie de centrale à charbon qui vit le jour à Rasken est la centrale à charbon dite sous-critique. Son fonctionnement est très simple. La première étape est de broyer le charbon en une fine poudre afin de faciliter la combustion. Une fois le charbon réduit en poudre, il est ensuite injecté dans la chaudière afin d’y être brûlé, la température montant entre 1300 et 1700 °C. La chaleur libérée par cette combustion va chauffer un réseau de tubes dans lesquels circule de l’eau. Sous l’effet de la chaleur, l’eau liquide va se vaporiser. Dans ce type de centrale, la vapeur se forme typiquement à une pression comprise entre 160 et 200 bars et à une température de 500 à 600 °C. Une fois formée, la vapeur est envoyée dans une turbine haute pression. Après une première détente, elle est réchauffée puis envoyée dans une turbine intermédiaire à plus basse pression. Enfin, elle finit sa course dans une turbine basse pression où elle achève son expansion. Après la turbine basse pression, la vapeur est envoyée dans un condenseur afin d’être retransformée en eau liquide. Cette eau est ensuite renvoyée vers la chaudière par des pompes d’alimentation pour recommencer un nouveau cycle. Les gaz, eux, passent par une série de filtres afin de retirer les éléments les plus nocifs. Sur certains types de centrales, il est nécessaire d’utiliser un désulfuriseur pour enlever le soufre des fumées.
Ces centrales sont objectivement les plus simples à construire et les moins chères. Cependant, en raison de leur ancienneté, elles accusent un rendement plutôt bas pour une centrale thermique, en effet, le rendement de ces centrales tourne autour de 35 %. Ce type de centrale fut abandonné en 1980 en raison de son faible rendement et donc de sa consommation accrue en combustible.
Centrale supercritique : La deuxième technologie à avoir vu le jour est celle des centrales à charbon dites supercritiques. Ces centrales sont une évolution des centrales sous-critiques. À cet effet, toute la partie broyage et combustion du charbon est la même. En revanche, ce qui va changer, ce sont les conditions dans lesquelles va se former la vapeur. À la différence des centrales sous-critiques, les centrales supercritiques fonctionnent… au-delà du point critique. C’est bien, vous suivez. Mais au final, c’est quoi le point critique ? Comme vous le savez tous, au niveau de la mer, l’eau bout à 100 °C, cela est dû à la pression d’1 bar au niveau de la mer. Mais plus on augmente la pression, plus on augmente la température nécessaire pour former la vapeur. Cependant, on ne peut pas monter indéfiniment et, à un stade donné, même si l’on continue à augmenter la pression, les états liquide et gazeux commencent à se confondre. Ce point critique est défini comme étant un point à 221 bars et 375 °C. Les centrales supercritiques sont donc des centrales capables de former de la "vapeur" au-delà du point critique. Les centrales de ce type fonctionnent typiquement avec des pressions de 250 à 300 bars et des températures de 550 à 600 °C. Ensuite, la partie turbine, condensation et fumée est quasiment la même, à part pour les turbines, qui doivent être dimensionnées pour encaisser la température et la pression plus importantes.
Cette augmentation de pression et de température permet une augmentation significative du rendement, passant de 35 à 40 %. Cette amélioration permet une réduction de la consommation de combustible pour produire la même quantité d’énergie et donc une réduction des émissions de CO2, passant de 1000 g/kWh à environ 850 g/kWh.
Centrale ultra supercritique : Ce type de centrale ne dispose que d’un seul représentant sur le sol Raskenois. Il s’agit de la toute dernière évolution en matière de centrale à charbon. Comme pour la centrale supercritique, la partie broyage et combustion est la même, et c’est encore une fois la formation de la "vapeur" qui va changer. En effet, pour une centrale ultra-supercritique, le fluide se forme à une pression supérieure à 300 bars et une température comprise entre 600 et 700 °C. Le fait de monter encore plus en température et en pression fait que le fluide est beaucoup plus dense et énergétique qu’une simple centrale supercritique ou sous-critique. Cette densité énergétique permet encore d’augmenter le rendement et de tutoyer les 50 % en laboratoire. Cependant, dans des conditions pratiques, les centrales Raskenoises ont un rendement de 45 %. Cette augmentation de rendement permet encore de réduire la consommation de charbon et les émissions de CO2, pour tomber à 750 g/kWh.
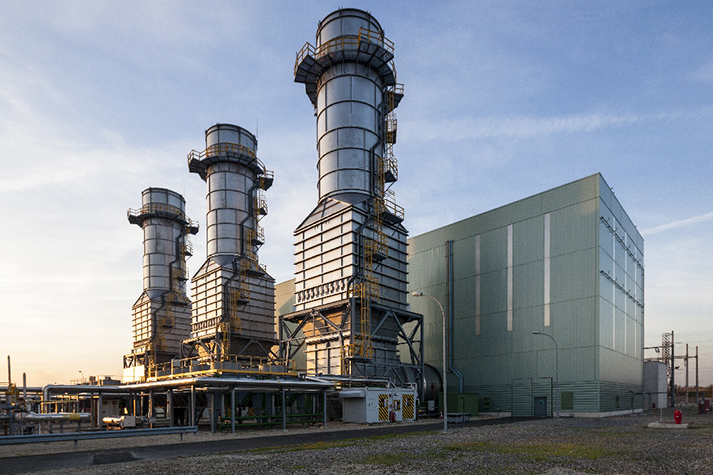
Les centrales à gaz sont le troisième type de centrale à voir le jour à Rasken, au même titre que les centrales à charbon ou à biomasse, ce sont des centrales thermiques donc qui brûlent du combustible pour produire de l’électricité. La différence entre les centrales au gaz et, par exemple, au charbon, c’est leur efficacité. En effet, les premières technologies de centrales à gaz ont un rendement à peine inférieur aux meilleures centrales à charbon actuelles. À titre d’exemple, une centrale à gaz simple, donc sans turbine à vapeur, a un rendement de 40 %, soit 5 % de moins que la centrale à charbon ultra-supercritique. Mais ce genre de technologie n’existe pas à Rasken, la première centrale à gaz du pays intégrant déjà un cycle de vapeur. À Rasken, il existe 3 technologies de centrales à gaz en service actuellement, technologies que nous allons détailler de la plus ancienne à la plus récente.
Centrale CCG classique : Une centrale CCG classique est le premier type de centrale à gaz qui a vu le jour à Rasken. Cette technologie intègre deux pôles de production électrique, la première est la turbine à gaz et l’autre est la turbine à vapeur, d’où le nom CCG pour Cycle Combiné Gaz. Son fonctionnement est assez simple : premièrement, de l’air est aspiré dans un compresseur afin de le faire monter en pression, typiquement de 10 à 30 bars, cette compression fait monter la température de l’air à environ 400°C. Une fois comprimé et chauffé, l’air est injecté avec le gaz naturel dans la chambre de combustion pour brûler et générer de l’énergie, les gaz chauds formés par la combustion atteignent une température dans la chambre de combustion de l’ordre de 1600°C. Les gaz chauds ainsi formés occupent plus de place que le mélange gaz naturel-air, ce qui fait augmenter la pression. Ce mélange de gaz de combustion à haute pression et haute température est dirigé vers une turbine à gaz pour la faire tourner. Cependant, sur les premières générations de CCG, les turbines ne pouvaient pas encaisser la chaleur des gaz de combustion, ainsi, en entrée de turbine à gaz, la température n’était plus que de 800 à 1000°C. L’énergie mécanique de rotation produite par la turbine est majoritairement utilisée pour faire tourner un alternateur et produire de l’électricité, mais une petite partie est redirigée vers les compresseurs afin de les faire tourner. À la sortie de la turbine, les gaz de combustion sont encore à très haute température, autour de 600°C, cette quantité d’énergie thermique encore disponible est alors redirigée vers une chaudière de récupération qui n’est ni plus ni moins qu’un échangeur de chaleur. Cette chaleur résiduelle est transmise à l’eau afin de produire de la vapeur d’eau, en sortie de chaudière, la température des gaz n’est plus que d’environ 125°C. Une fois formée, la vapeur est dirigée vers une succession de turbines afin d’alimenter le cycle vapeur ou cycle de Rankine. En sortie du cycle, la vapeur est complètement détendue et ne contient plus d’énergie, il faut alors la condenser pour la retransformer en liquide, une fois cela fait, elle est renvoyée vers la chaudière de récupération.
Ce type de centrale qu’on appelle CCG de première génération on typiquement un rendement de 60 %. Elle furent toute remplacé dans les années 90 par une autre technologie.
Schéma de fonctionnement simplifié d’une CCG classique :
Gaz naturel → Combustion → Turbine à gaz → Générateur électrique
XXXXXXXXXXXXXXX↓
XXXXXXXXXGaz chauds résiduels → Chaudière de récupération → Production vapeur
XXXXXXXXXXXXXXXXXXXXXXXXXXXXXXXXXXXXXXXXXXXXXXXXXXXXXXXXXX↓
XXXXXXXXXXXXXXXXXXXXXXXXXXXXXXXXXXXXXXXXXXXXXXXXXXXXXTurbine à vapeur → Générateur électrique secondaire
XXXXXXXXXXXXXXXXXXXXXXXXXXXXXXXXXXXXXXXXXXXXXXXXXXXXXXXXXX↓
XXXXXXXXXXXXXXXXXXXXXXXXXXXXXXXXXXXXXXXXXXXXXXXXXXXXXCondenseur → Eau condensée → Pompe → retour chaudière de récupération
Centrale CCG haute température : Les CCG haute température sont quasiment identiques aux CCG classiques, la seule différence notable, c’est le fait que la turbine à gaz soit maintenant en capacité de résister à de plus hautes températures. Sur la première génération de CCG, les matériaux composant la turbine ne pouvaient pas encaisser les 1600°C, mais le développement de nouveaux matériaux permit de résister à cette température. Cela permit, dans les années 90, de mettre à niveau toutes les centrales Raskenoises, leur permettant d’augmenter leur rendement et donc leur production électrique.
Le rendement typique des CCG haute température, donc de deuxième génération, est typiquement autour des 65 %. Cependant, de la même manière que celle-ci a remplacé les CCG de première génération, les CCG haute température devraient se voir remplacer par la troisième et dernière technologie de centrales à gaz développée à Rasken.
Centrale Superphénix : Le principal problème dans une centrale thermique qui limite le rendement, c’est l’air. En effet, dans l’air, seulement 21 % est utile pour la combustion, le reste, principalement de l’azote, agit comme une éponge à énergie. Cette éponge empêche la température de dépasser un certain seuil, par exemple, pour le gaz naturel, cette limite est de 1500°C. Le raisonnement derrière Superphénix est simple : si l’azote nous empêche de monter plus haut en température et donc en rendement, alors on va se séparer de l’azote. C’est ce que fait Superphénix, cette centrale unique en son genre effectue ce que l’on appelle de l’oxy-combustion, c’est-à-dire de la combustion dans de l’oxygène pur. Grâce à cela, les températures ne sont plus limitées par l’azote. Ainsi, la température dans la chambre de combustion monte au maximum à 3100°C, soit plus de deux fois plus haut que sur les CCG classiques. Le fonctionnement de Superphénix, bien que plus complexe, reste tout de même assez simple.
Premièrement, en dehors de la centrale, se trouvent des unités de production d’oxygène pur à très basse consommation afin de ne pas trop pénaliser la production électrique. Pour Superphénix, nous utilisons une combinaison de systèmes à Adsorption par Balayage de Pression et de Membranes à Échange Gazeux. Comme nous l’avons dit, nous ne voulons pas que l’azote freine la combustion. Ainsi, la solution la plus logique serait la distillation cryogénique permettant d’atteindre une pureté supérieure à 99,5 %, cependant, ce procédé est très énergivore et pourrait compenser les gains de puissance apportés par l’oxy-combustion. Ainsi, pour Superphénix, nous avons utilisé un astucieux agencement de technologies basse consommation qui, indépendamment, ne permettent pas d’atteindre une pureté comparable à la distillation cryogénique, mais qui, mis ensemble, peuvent s’en rapprocher. Pour produire l’oxygène, nous avons deux étages de séparation : premièrement, des membranes permettent de séparer une partie de l’azote et d’augmenter la concentration en oxygène à 40-50 %. Le deuxième étage de séparation consiste en une Adsorption par Balayage de Pression afin de concentrer l’oxygène jusqu’à 99 % pour une consommation de 130 kWh par tonne d’oxygène contre plus de 200 pour une distillation cryogénique.
Une fois l’oxygène pur obtenu, il est injecté en même temps que le gaz naturel dans la chambre de combustion. La température maximale atteinte lors de la combustion est de 3100°C, cette température est bien trop élevée pour n’importe quel matériau. Ainsi, avant même la turbine à gaz, de l’eau est injecté afin d’abaisser la température au environ de 2000°C, bien que cela abaisse la température et donc le rendement, c’est compensé par l’ajout de l’eau. Cette eau supplémentaire qui est donc sous forme de vapeur ajoute donc de la matière au flux de gaz contrebalançant en parti la baisse de rendement du à la baisse de la température.
Une fois la température abaissée à 2000°C, le gaz de combustion (majoritairement du CO2) est envoyé dans la turbine à gaz afin d’alimenter le cycle gaz (Brayton) très haute température. Ce flux de gaz à très haute température et haute pression, autour de 30 bars, est détendu dans la turbine. Cela met en mouvement ses pales qui entraînent à leur tour l’arbre de rotation, lequel entraîne lui-même l’alternateur. En sortie de turbine, les gaz contiennent encore une grande quantité d’énergie, la température étant encore de 800°C. Ce flux de gaz est alors envoyé dans une chaudière de récupération, produisant alors non pas de la vapeur, mais un fluide Ultra-Supercritique autour de 700°C pour 300 bars. Cette "vapeur" est alors envoyée dans des turbines afin d’être détendue et de produire de l’électricité. Une fois complètement détendue, la vapeur est alors condensée puis réinjectée dans le circuit. Enfin, l’oxy-combustion permet également une capture facilitée du CO2 grâce à sa pureté.
Grâce à l’oxy-combustion et au cycle de vapeur Ultra-Supercritique, les centrales de type Superphénix sont en capacité d’atteindre un rendement exceptionnel de 75 %.
Cependant, ce n’est pas fini, en effet, les centrales de type Superphénix disposent d’un autre atout dans leurs manches. Une évolution majeure de ce type de centrale par rapport à ses sœurs est l’intégration d’un mode de surpuissance. Ce mode de surpuissance est le résultat d’une combinaison de quatre astuces.
Premièrement, la centrale est en capacité d’injecter plus de combustible et d’oxygène que dans son fonctionnement normal. Ce combustible supplémentaire permet alors une augmentation de la puissance. La deuxième astuce consiste à injecter plus de vapeur d’eau dans la chambre de combustion. On pourrait se dire que cela va baisser la puissance, mais en fait non, car la puissance d’une turbine est directement liée à la quantité de matière en expansion qui la traverse. L’injection de vapeur d’eau augmente alors cette quantité de matière. De plus, l’injection de vapeur d’eau améliore le mélange air/carburant et stabilise la flamme. Cela réduit la formation de points chauds et améliore la propagation de la flamme, rendant la combustion plus homogène. Il en résulte moins de pertes thermiques et une combustion plus efficace. Enfin, cela permet également de réduire légèrement la température de la combustion, compensant ainsi dans une certaine mesure l’augmentation de la température due aux autres astuces. La troisième astuce consiste tout simplement à injecter un combustible avec un pouvoir calorifique plus important. Pour Superphénix, ce combustible, c’est l’hydrogène. Cela permet de booster la puissance sur une certaine durée. Enfin, la dernière astuce va de pair avec la première : elle consiste tout simplement à suralimenter en oxygène la chambre de combustion afin de pouvoir brûler plus de carburant.
Au final, qu’obtient-on ? Si l’on prend chaque astuce indépendamment, la surinjection de carburant ou Peak Firing permet une augmentation de la puissance d’environ 10 % en augmentant la température globale de 200°C. L’injection de vapeur d’eau, elle, permet de réduire la température d’environ 300°C en augmentant la puissance de 20 %. La troisième astuce, qui consiste en l’injection d’hydrogène, augmente la puissance de 15 %, mais augmente la température de 400°C. Enfin, la dernière astuce permet une augmentation de la puissance de 5 % pour une augmentation de température d’environ 100°C.
Cela donne, si l’on combine toutes les astuces, une augmentation de la puissance de 50 % avec une augmentation de la température de 400°C, poussant la température maximale à 3500°C. Ce boost est conçu pour pouvoir faire face aux augmentations rapides et importantes de la consommation. En effet, si la centrale fonctionne à sa capacité maximale de 1800 MW électriques et qu’une puissance supplémentaire est requise, les opérateurs activent ce boost et poussent la centrale à 2700 MW en une dizaine de minutes. Cependant, les composants de la centrale ne sont pas conçus pour résister longtemps à une telle température. Ce boost de puissance est donc limité dans le temps : passé une heures, on estime que le risque de destruction totale de la centrale est très important.
?????????? : Enfaîte, nous vous avons menti, il existe non pas 3 mais 4 technologies de centrales à gaz sur le territoire Raskenois. Cependant, cette quatrième technologie est encore en développement, c’est pourquoi nous ne l’avons pas incluse au début. Cette technologie est en fait une évolution de la centrale à gaz Superphénix qui pourrait potentiellement augmenter le rendement de 7 points de la centrale. Actuellement, Superphénix, pour ne pas s’auto-détruire à cause de la chaleur intense, injecte de l’eau dans les gaz de combustion avant la turbine à gaz afin de réduire leur température. Cette méthode éprouvée fonctionne, mais n’est pas optimale. En effet, elle induit une réduction du rendement global de la centrale. Afin de remédier à cela, il faudrait trouver un moyen de réduire la température des gaz à 2000°C sans pour autant injecter de l’eau dans les gaz d’échappement. L’une des solutions que nous avons trouvées est de rajouter un étage de formation de vapeur.
Actuellement, dans une centrale Superphénix, le gaz brûle, puis est refroidi grâce à de l’eau avant de passer dans une turbine à gaz. Une fois la turbine à gaz passée, la chaleur restante est utilisée dans une chaudière de récupération afin de former de la vapeur dans un état ultra-supercritique. L’objectif ici serait de faire passer les gaz de combustion dans une autre chaudière de récupération avant même la turbine à gaz afin d’abaisser la température de 3100 à 2000°C. Étant donné la différence de température plus importante, cette chaudière de récupération produirait de la vapeur non pas ultra-supercritique, mais hyper-supercritique aux alentours de 1000°C pour 500 bars. Cette "vapeur" contiendrait une quantité exceptionnellement élevée d’énergie, permettant, de par sa température et sa pression, un rendement tout aussi exceptionnellement haut pour un cycle de vapeur. On parle de 60 à 65 % contre 55 % pour un cycle ultra-supercritique. Si une chaudière très haute température est plus efficace, c’est pour plusieurs raisons, mais pour faire simple :
La récupération thermique via une chaudière haute température (échangeur thermique organisé) est bien plus efficace parce qu'elle préserve la qualité de l'énergie (exergie élevée), limite les pertes entropiques, et permet d'exploiter cette énergie thermique à un niveau élevé (900–1000 °C, hyper-supercritique). Au contraire, l'injection directe d’eau génère un refroidissement chaotique, dilue l’énergie thermique, augmente fortement l’entropie, et conduit à des pertes significatives de potentiel énergétique exploitable.
Cependant, cela pose un autre problème. Avant, la température était abaissée par injection d’eau, mais maintenant, c’est la surface de la chaudière qui est en contact avec la chaleur. Cette surface doit donc être en capacité de résister à celle-ci. C’est ce problème qui fait que, quand bien même la recherche sur cette méthode ait commencé en parallèle de l’injection d’eau pour refroidir les gaz de combustion avant la turbine dans le cadre du projet Superphénix, la centrale actuelle n’en soit pas équipée. Cependant, il est prévu depuis le début du projet de remplacer à terme l’injection d’eau par la chaudière de récupération primaire. C’est d’ailleurs pour cela que, si vous avez eu la chance de visiter la centrale, les salles semblent bizarrement grandes. En fait, tout était prévu depuis le début. Ainsi, le bâtiment fut dimensionné pour pouvoir accueillir à terme les infrastructures supplémentaires.
Mais donc, aujourd’hui, où en sommes-nous ? Effectuons-nous toujours des recherches sur cette chaudière haute température ? Eh bien oui, et cela pour plusieurs raisons. La résistance thermique n’est pas le seul point à prendre en compte. En effet, actuellement, des matériaux résistants à plus de 3000°C existent, comme par exemple le carbure de tantale ou le carbure d’hafnium. Cependant, ces matériaux ont aussi la particularité d’avoir une conductivité thermique très basse. Ainsi, si nous devions faire un échangeur avec cela, il aurait des dimensions titanesques, de plusieurs centaines de mètres, le rendant de facto inutilisable. On estime que la recherche sur ces matériaux devrait se terminer à l’horizon 2020 et qu’un premier test sur le démonstrateur industriel du site de Tremblay devrait avoir lieu d’ici 2022. Si les tests s’avèrent concluants, alors un déploiement à grande échelle sur Superphénix, voire sur les autres centrales du même type qui seront construites d’ici 2024, pourrait être envisagé. À terme, si le projet porte ses fruits, nous pouvons espérer un gain de rendement maximal de 10 %. Pour Superphénix, cela représenterait une puissance électrique de 2040MW.
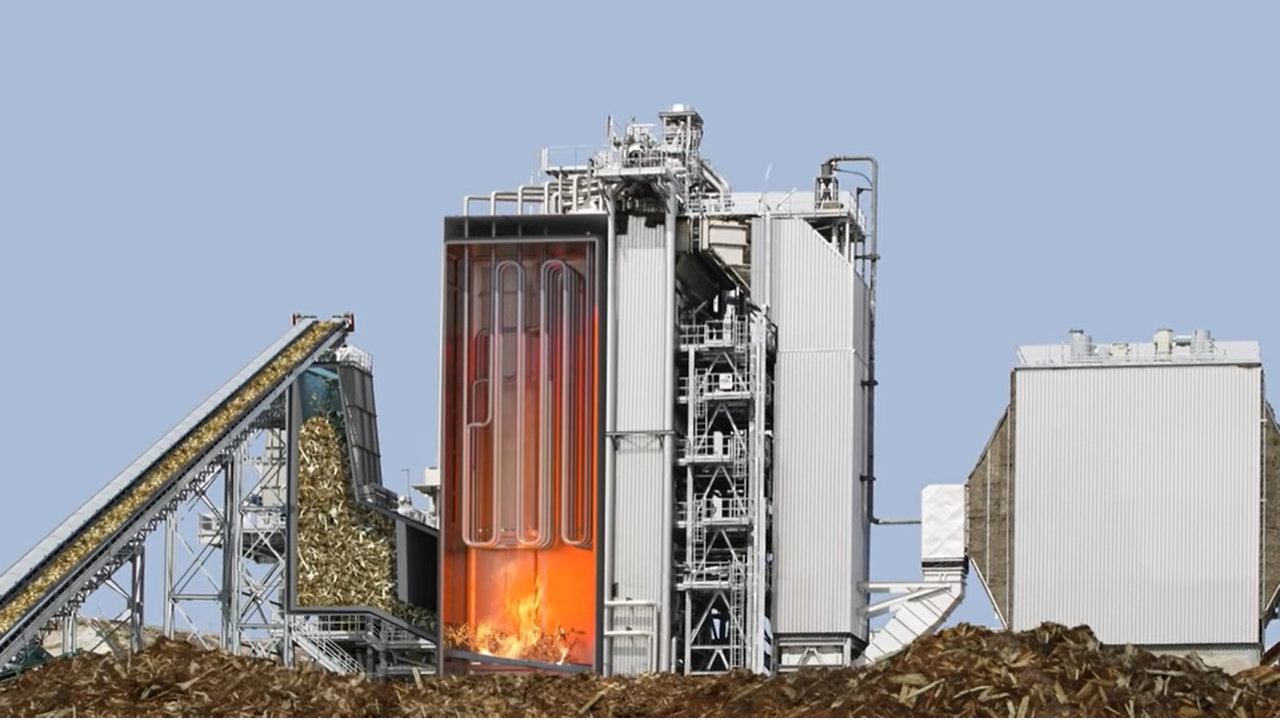
Les centrales à biomasse sont les centrales les plus anciennes avec celles à charbon. Cependant, elles ne furent pas construites avec l’objectif premier de générer de l’électricité, mais de se débarrasser de déchets organiques dont on ne savait pas quoi faire. Pour se débarrasser de ces déchets, on aurait pu simplement les brûler. Cependant, quitte à les brûler, autant s’en servir pour produire de l’électricité. Il existe sur le territoire raskenois trois technologies de centrales biomasse, dont une seule est encore utilisée de nos jours.
Centrale biomasse à combustion directe : Les centrales biomasse à combustion directe sont les centrales les plus simples à construire ainsi que les plus répandues. Afin de produire de l’électricité, la biomasse est entreposée un certain temps dans des endroits spéciaux afin de faire baisser son taux d’humidité. Généralement, la biomasse contient un taux d’humidité compris entre 40 % pour du bois fraîchement coupé et jusqu’à 70 % pour des déchets verts comme des feuilles. Afin d’être utilisable dans ce type de centrale, il est nécessaire de faire baisser cette humidité au minimum en dessous des 20 %, car généralement, la combustion avec de l’eau n’est pas très efficace. Une fois séchée, la biomasse est envoyée à la centrale, mais avant d’être brûlée, celle-ci va être broyée afin de faciliter la combustion. Ensuite, la biomasse est envoyée dans la chambre de combustion au moyen d’un convoyeur ou d’une vis sans fin. Une fois dedans, la biomasse est brûlée, générant de la chaleur. Cette chaleur est ensuite utilisée de la même manière que dans une centrale au charbon pour faire de la vapeur, vapeur qui va entraîner une turbine pour produire de l’électricité.
Bien que très simple à mettre en œuvre, ce type de technologie n’est pas optimal. En effet, son rendement dépasse rarement les 30 %, ce qui fait que de grandes quantités de biomasse sont nécessaires pour produire de grandes quantités d’énergie. Cela explique également pourquoi Rasken ne dispose pas de plus de ce genre d’installations, car l’objectif était de se débarrasser des déchets et non de raser des forêts pour produire de l’électricité. Ce type de centrale n’est plus utilisé depuis 1948 à cause de son efficacité limitée. Elle fut remplacée par une autre technologie qui, bien que plus complexe, dispose de meilleures performances.
Centrale biomasse à gazéification : Cette technologie, bien que plus complexe que la combustion directe, remplaça rapidement celle-ci, la première centrale de ce type voyant le jour seulement deux ans après la fermeture de la dernière centrale à combustion directe. Cette technologie est basée sur un principe totalement différent de celui précédemment présenté. Là où avant on brûlait directement la biomasse, ici on cherche à transformer cette biomasse en gaz qui, eux, seront brûlés. Comme pour la combustion directe, la biomasse doit être séchée afin d’atteindre un taux d’humidité de 20 %. Une fois cela fait, la biomasse est envoyée dans la première étape de la gazéification, qui consiste à retirer l’humidité restante. Cette étape se passe généralement autour des 150°C. Une fois l’humidité résiduelle éliminée, la biomasse entre dans la deuxième étape : la pyrolyse. Cette étape consiste à chauffer la biomasse entre 200 et 600°C en l’absence d’oxygène, entraînant une décomposition thermique de la biomasse sans pour autant la brûler. L’objectif de cette étape est de produire des gaz volatils comme l’hydrogène, le monoxyde de carbone et le méthane. En parallèle, la biomasse va se transformer en charbon. La troisième étape est l’oxydation/combustion partielle entre 800 et 1400°C. À ce stade, une légère quantité d’oxygène est introduite afin de brûler partiellement le charbon et de générer de la chaleur pour maintenir le processus. La quatrième étape est la réduction et consiste à faire réagir le carbone restant avec de l’eau et du dioxyde de carbone afin de produire du syngas. Ce qu’on appelle le syngas est en fait un gaz de synthèse combustible composé en grande majorité d’hydrogène, de méthane et de monoxyde de carbone. Cependant, ce gaz de synthèse contient encore des impuretés nécessitant de le filtrer avant de l’introduire dans la chambre de combustion.
Une fois le gaz produit, il existe plusieurs méthodes pour produire de l’électricité. La première est d’utiliser le gaz comme carburant dans un moteur à combustion interne. Cependant, cette méthode est plus adaptée aux installations de faible puissance, autour de 10MW. La deuxième solution est d’utiliser le gaz dans une turbine, comme pour les centrales à gaz classiques. C’est cette méthode qui est utilisée à Rasken. Ce genre d’installation a typiquement un rendement de l’ordre de 40 %. Cependant, il est également possible, au-delà d’une turbine à gaz simple, de produire de la vapeur avec un cycle combiné gaz (CCG), ce qui permet d’atteindre un rendement supérieur, de l’ordre de 55 %. Si cette méthode CCG n’est pas utilisée à Rasken, c’est à cause de la troisième technologie que nous allons vous présenter.
Centrale biomasse à cogénération : Ce type de centrale n’est pas une technologie différente, mais simplement une évolution. En effet, une fois brûlés et utilisés dans la turbine, les gaz contiennent encore de l’énergie thermique. L’une des solutions pour récupérer cette chaleur est de produire de la vapeur. Cependant, à Rasken, nous avons fait les choses différemment. En effet, dans les années 1990, quand les deux installations raskenoises ont subi de grands travaux pour les moderniser, il fut décidé de transformer ces centrales en centrales à cogénération afin de produire, en plus de l’électricité, de la chaleur. Cette chaleur est ensuite envoyée soit vers un réseau de chaleur urbain, soit vers des sites industriels ayant besoin de vapeur. Grâce à la cogénération, les centrales biomasse peuvent atteindre des rendements bien plus élevés. En effet, nos centrales ont actuellement un rendement globale de l’ordre de 80 %.
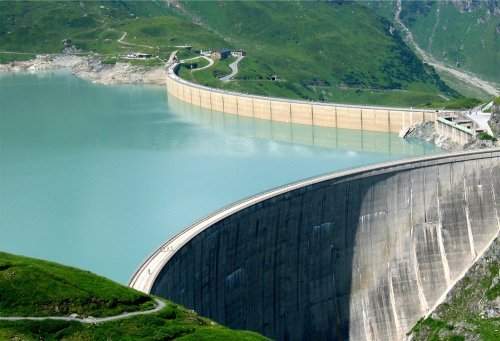
Pour exploiter la force de l’eau, il existe différentes technologies, mais la plus répandue est celle des barrages hydroélectriques. Cependant, au sein même de cette technologie, il existe plusieurs sous-catégories. Il y a d’abord les barrages dits au fil de l’eau, qui exploitent une différence de hauteur entre l’amont et l’aval du barrage, typiquement inférieure à 20 mètres. Viennent ensuite les barrages de moyenne chute, qui exploitent une différence de hauteur comprise entre 20 et 300 mètres. Pour finir, il y a les barrages haute chute, qui exploitent une différence de hauteur supérieure à 300 mètres. À Rasken, nous utilisons deux types de technologies : les barrages de moyenne chute, représentés par Lozf, et les barrages haute chute, représentés par Osterwald 1 et 2. Le but ultime de tout barrage est de transformer l’énergie potentielle de pesanteur de l’eau en électricité (l’énergie potentielle de pesanteur est l’énergie que possède un objet du à une différence de hauteur), cependant, en fonctionne de la hauteur de chute, différente turbine sont utilisé.
Barrage haute chute, turbine Pelton : Les barrages de retenue utilisent une différence de hauteur importante (>300 mètres), mais un débit faible. Pour cela, ils doivent utiliser ce que l’on appelle une turbine Pelton. Ces turbines sont spécialement conçues pour les chutes d’eau de grande hauteur et de faible débit. Ce type de barrage, caractérisé par les grands lacs qu’il forme, a un fonctionnement plus complexe que celui d’un barrage de moyenne hauteur.
Une fois l’eau retenue grâce au barrage, celle-ci est redirigée grâce à une conduite forcée. À l’entrée de cette conduite, on retrouve différentes grilles afin d’empêcher que des débris, comme des morceaux de roche, ne pénètrent à l’intérieur et endommagent la turbine. Une fois dans la canalisation, l’eau est dirigée vers la salle des turbines en contrebas, mais avant d’entrer en contact avec la turbine, elle passe par une série d’injecteurs, généralement compris entre 1 et 5. Les injecteurs servent à concentrer le flux d’eau et à augmenter sa vitesse, parfois jusqu’à 100 mètres par seconde. En plus de concentrer et d’accélérer le flux d’eau, ils ont aussi un rôle de régulateur de débit, permettant d’ajuster en permanence la puissance.
Ensuite, une fois que l’eau est à l’air libre, elle vient frapper ce que l’on appelle des augets (petites coupelles) disposés sur la roue de la turbine. L’impact de l’eau sur ces augets incurvés provoque la mise en rotation de la roue. Enfin, la rotation de la turbine entraîne l’alternateur, ce qui permet de générer de l’électricité. Une fois l’eau dépourvu d’énergie, elle est évacué dans la rivière.
Ce type de turbine est conçu pour accepter des débit plutôt faible, mais compense ce faible débit par une différence de hauteur acceptable beaucoup plus importante. Le rendement de c’est turbine se trouve au alentour de 90 %
Barrage de moyenne chute, turbine Francis : La première technologie de barrage à avoir vu le jour sur le territoire Raskenois fut celle des barrages de moyenne hauteur, représentée par Lozf. Ce type de barrage utilise ce que l’on appelle une turbine Francis. À la différence d’une turbine Pelton, qui utilise uniquement la vitesse de l’eau et son impact sur les augets, une turbine Francis exploite à la fois l’énergie cinétique et l’énergie de pression du fluide. Comme pour les barrages à haute chute, les barrages de moyenne chute canalisent l’eau du fleuve ou de la rivière vers une salle des turbines. Cependant, à la différence des turbines Pelton, où la turbine est à l’air libre et donc à pression atmosphérique, la turbine Francis est intégralement immergée dans l’eau, lui permettant ainsi d’exploiter la pression du fluide.
Premièrement, l’eau entre dans le distributeur et est orientée par ce que l’on appelle des directrices. Ces directrices permettent de régler l’angle du flux d’eau afin d’optimiser les performances de la turbine. Après les directrices, l’eau pénètre dans la roue de la turbine de manière radiale, c’est-à-dire de l’extérieur vers l’intérieur. En traversant les aubages courbes de la roue, l’eau cède son énergie cinétique et sa pression. Cette énergie permet à la roue de tourner à grande vitesse, typiquement entre 100 et 1000 tours par minute. Étant connectée à l’alternateur, la rotation de la roue entraîne la production d’électricité.
Une fois que l’eau a perdu la majorité de son énergie, elle quitte la turbine axialement par un tube de diffusion que l’on nomme tube de fuite. Ce tube de diffusion permet de récupérer une partie de l’énergie résiduelle contenue dans l’eau, améliorant ainsi le rendement. En sortie du tube de diffusion, l’eau est rejetée en aval de la rivière.
Ce type de turbine accepte des débits plus importants pour pallier la différence de hauteur plus faible par rapport aux turbines Pelton. Le rendement des turbines Francis est similaire à celui des Pelton, tout en étant légèrement supérieur : aux alentours de 94 % contre 90 % pour les Pelton.
Station de Transfert d’Énergie par Pompage (STEP) : Cette technologie, qui n’en est pas vraiment une à part entière, est en fait l’un des seuls, voire le seul moyen permettant de stocker de l’électricité de manière massive. Nombre de pays souhaitant effectuer leur transition énergétique des énergies fossiles vers les renouvelables rencontrent ce problème. Le problème étant que ces énergies sont dites intermittentes, c’est-à-dire que leur production est variable dans le temps et que nous n’avons souvent pas le contrôle dessus. Ainsi, pour s’assurer que le réseau électrique reste stable dans le temps, il faut surdimensionner les appareils de production afin de stocker l’énergie quand les générateurs fonctionnent à leur pleine capacité, puis restituer cette énergie stockée quand il n’y a plus de vent ou de soleil.
Le problème étant que l’électricité est difficilement stockable, on pense en premier lieu aux batteries. Cependant, elles sont chères et ont une durée de vie limitée, ce qui rend le stockage de grandes quantités d’électricité très compliqué. Une autre solution est de produire de l’hydrogène par électrolyse quand il y a une surproduction d’électricité, puis de faire réagir cet hydrogène dans une pile à combustible pour récupérer l’électricité. Le problème de ce genre de technologie est leur rendement très faible : la pile à combustible seule a un rendement de l’ordre de 50 %, cependant, à cela, il faut ajouter le rendement de l’électrolyseur qui est de l’ordre de 70 %, au final, le rendement global de l’installation est de 35 %. On peut cependant augmenter quelque peu ce rendement avec une centrale à gaz classique ayant un rendement supérieur à celui d’une pile à combustible.
On en arrive donc à cette conclusion : si l’on veut stocker de l’énergie, il faut soit débourser des milliards en batteries, soit surdimensionner d’un facteur 3 les générateurs si l’on utilise de l’hydrogène. Cependant, comme dit plus haut, le meilleur système de stockage, ce sont les STEP, qui ont un rendement de l’ordre de 80 %. Mais concrètement, qu’est-ce qu’une STEP ? Une STEP est en fait un barrage réversible, c’est-à-dire que lorsque l’on se retrouve en situation de surproduction, on pompe de l’eau en direction d’un réservoir en altitude, puis, en cas de sous-production, on laisse l’eau redescendre comme dans un barrage classique.
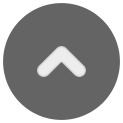